Sustainability down the line: from the charging station to the new lighting system
4-minute read
In the idyllic Sauerland region, surrounded by lush meadows, variegated forest landscapes and clean watercourses, this is where SCHELL is at home. The company actively integrates sustainability into its business – from the exemplary waste separation in its offices to the sustainable production of long-lived products. Both of its factories, including the sustainable production of angle valves, are located close to one another here in Olpe – this proximity cuts the costs of logistics and unnecessary environmental pollution while keeping carbon footprints small. As with the surroundings, so, too, the company: unspoilt nature and, above all, clean water are right at the top of its agenda.
Yet SCHELL is not only concerned about the sustainability of the water that flows through piping to the fitting, but also about the clean power that is transported by electrical cabling. Which is why only 100 percent green electricity from sustainable energy sources is used in the company – and now also at the charging points that offer convenient charging both for the company’s own electric vehicles, and those from visitors and customers.
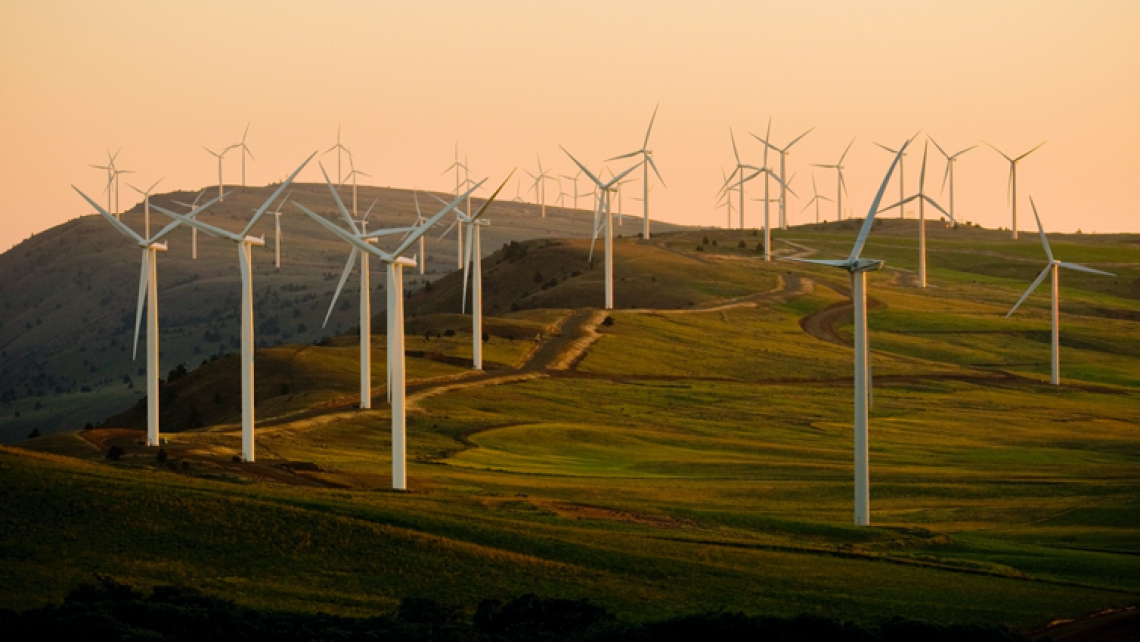
New EVs and charging stations
Electric vehicles have been added to the SCHELL company fleet. These EVs can be conveniently ‘filled up’ with green electricity on the company premises at five MENNEKES AMEDIO Professional 22 charging stations, each offering two charging points. The ‘plug & charge’ function offered provides a simple way to get power into the vehicle without a special charging card or app — ideal for everyday use since the authorisation step is automated. One charging station is reserved for customers and visitors. This sustainable project received funding from the ‘Low Emission Mobility’ programme in North Rhine-Westphalia.
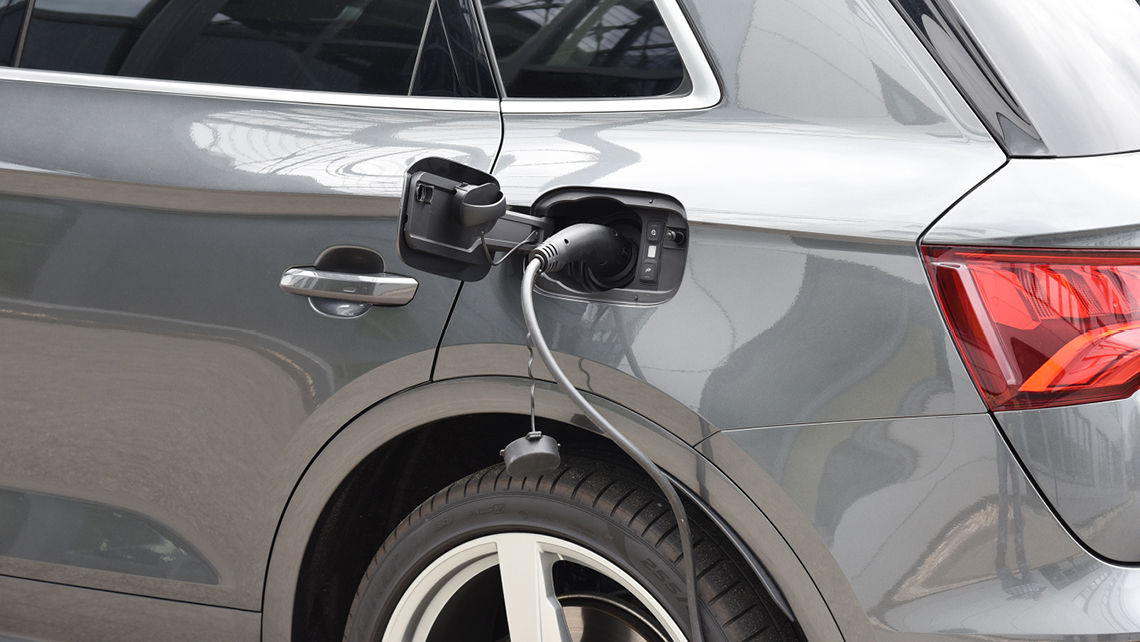
Power-saving lighting in production
One innovation has also made production more sustainable, with the existing T8 luminaires being replaced by a new, LED-based lighting system. All in all, around 700 fluorescent tubes in our production facility have now been replaced by modern LED modules, thereby creating a sustainable and efficient lighting installation. Alongside these energy-saving, efficient and long-lived LEDs, which are also virtually maintenance-free, a daylight-sensitive light control system has also been integrated, which also helps to cut power consumption. Overall, this adds up to around a 65 percent saving on the lighting energy budget. This project received funding from the Federal Ministry for Economic Affairs and Energy. We’ve also completed energy-related refurbishments to our façade lighting and outdoor logo lighting.
The latest trends in recycling and waste separation
SCHELL considers itself duty-bound to apply the cradle-to-cradle principle for a systematic, end-to-end circular economy. This cradle-to-cradle approach means that products are manufactured in a loop, with the aim of minimising their impact on nature and the climate. This also involves environmentally conscious production and the use of renewable energy sources. Complementing the use of green power at SCHELL, the company also takes steps to ensure that as many materials as possible are recycled. As one example, brass fittings can be recycled almost entirely and thereby returned to the raw material loop, while the brass swarf and chippings created during production are also managed in the loop.
Find out more about sustainability at SCHELL in Part 1 and Part 2!